
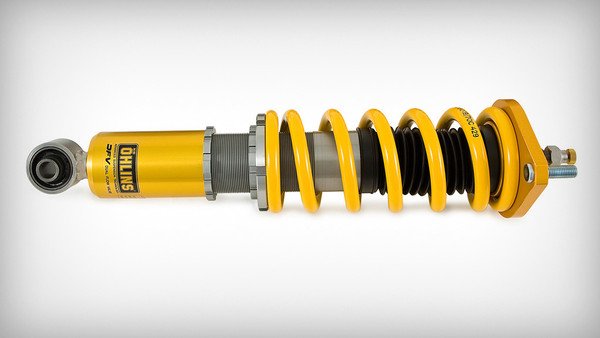
On both front and rear suspension geometries on the Lister, the inboard pivot axes of the top and bottom wishbones are splayed in plan view.

The option to counter this by rising-rate rear springing can give traction problems over bumps and kerbs – why I tend to avoid it. The problem then is that the roll stiffness split between front and rear axles moves progressively forward as speed increases, which can lead to high-speed understeer. Unless you use rising-rate springing and/or bump rubbers, you will quickly destroy your crucial front underbody. Rising-rate is necessary at the front, because the minimum ride height at the extreme front of the car will be around 15mm (0.6in) lower than at the rear (depending on front underbody detail), and braking causes the nose to dip further. I would have preferred falling-rate on the front anti-roll bar, to compensate for the rising spring rate at high speed when aero loads are compressing the spring, but this proved a little difficult to package working in CAD – it may be possible with a physical car to work around. Whereas on the front suspension of the Lister there is a measure of spring/damper rising-rate in the rocker geometry, the rear rocker has zero rising-rate on spring/damper and anti-roll bar. Many have mentioned the complexity of the Lister’s suspension although in fact it uses no more components than a conventional system.
